Self-healing aircraft wings: a dream or a possibility? Understand article
Taking inspiration from nature’s amazing ability to heal wounds, this biology-inspired technology could create aircraft wings that fix themselves.
A wing is ripped from the aircraft; the cabin roof is swept off, leaving passengers exposed to unpressurised air; or a plane disintegrates mid-flight: sadly these are all real examples of the catastrophic consequences of mechanical failure in an aircraft.
The immediate causes of these events, however, were not substantial: there was no collision with another aircraft, no bird strike, not even severe turbulence. The culprits were minute fatigue cracks within the aircraft structure, invisible to the naked eye. Modern inspection and maintenance requirements mean that microscopic damage like this is likely to be detected before it has serious consequences.
Currently the repair of such damage can be as crude as gluing or bolting a patch over the damaged area. Scientists at the University of Bristol, UK, however, have developed a novel way to repair small-scale damage to aircraft wings. Involving both catalysis and polymerisation, this new technology is an example of how important chemistry can be in our everyday life.
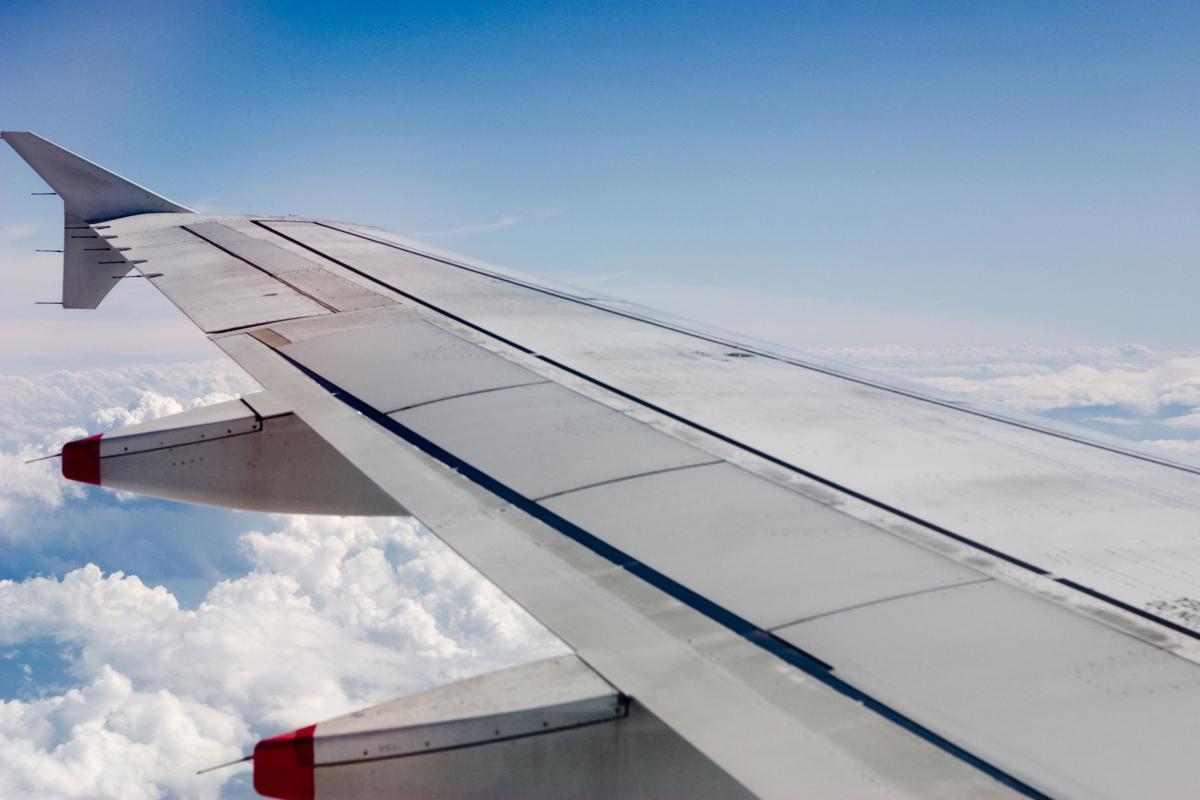
The downside of modern composite materials
To withstand aerodynamic forces, an aeroplane must be strong, stiff, durable and lightweight. Early aeroplanes used fabric and wood before metal alloys of aluminium and steel became commonplace. Now, carbon-fibre reinforced composites are the modern materials of choice for aerospace structures such as aircraft and for wind turbines. These composites are similar to natural materials such as wood, in which long cellulose fibres are held together by lignin. In these new materials, however, a homogenous matrix component is reinforced by a stronger and stiffer carbon fibre constituent. This is ideal for aircraft wings and wind turbines, which must be light but also strong enough to withstand extreme pressure and other stresses, such as bird strikes. Although these characteristics make reinforced composites better suited for building aeroplanes than the traditional metal alloys, there is one drawback: damage to composite structures is more difficult to detect and repair.
To find a solution, the Bristol scientists have taken their inspiration from nature. Professor Duncan Wass and his team considered what happens when we cut a finger: we bleed, a scab is formed to protect the damaged region, and eventually the wound is repaired. Could such an approach be used to repair man-made structures? Working in the laboratory in collaboration with a team of aerospace engineers led by Professor Ian Bond, the Bristol team may have found a way to do just this.
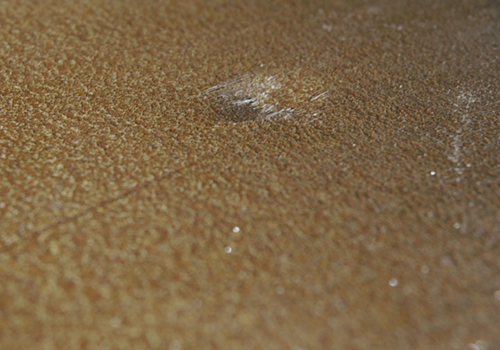
Image courtesy of Duncan Wass
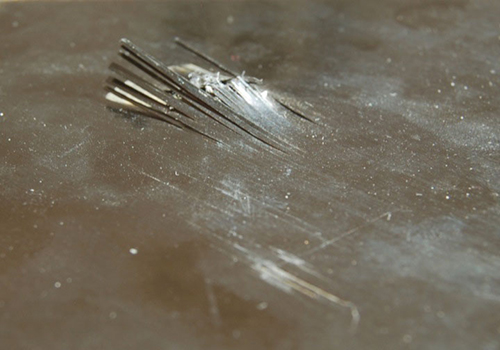
Image courtesy of Duncan Wass
How the new technology works
The key to the problem lies in the initial production of the composite, to which the researchers added microcapsules filled with a liquid. These sealed containers are so small that they look like a powder. In an aircraft wing made from such a composite material, damage causes these microcapsules to rupture, releasing the liquid into the resulting cracks. A rapid reaction takes place and the chemicals harden, filling in and ‘gluing’ together any cracks. How this works involves two key areas of chemistry: polymerisation and catalysis.
The wound is sealed as a result of polymerisation reactions in which small molecules, termed monomers, are joined together in a long chain, called a polymer. The monomers released from the microcapsules contain reactive chemical groups called epoxides (figure 3). These groups are three-membered ring structures that can be opened by an appropriate catalyst; once one ring is opened, it will react with another, which opening this second ring and joining the two together. The second ring will then react with a third, and so on, until a polymer is created. By controlling the exact structure of these monomers, researchers ensure that the polymer chains undergo a process called curing, forming a highly cross-linked network that has properties very similar to those of the original, undamaged composite. This ‘healing’ can recover up to 100% of the material’s mechanical strength.
As with most chemical reactions, the speed of curing is temperature dependent. Think of the reaction in terms of bond breaking and bond making. Heating provides more energy so the molecules move faster and are more likely to collide. This means that more chemical bonds are broken in the reactants so that new bonds can be formed in the products. The time it takes to repair a crack will therefore depend on the temperature of the material. If the aircraft is on a runway in Barcelona, Spain, in summer, it would probably heal in a couple of hours, but on a runway in Reykjavik, Iceland, in winter, it could take between 24–48 hours.
Even in the heat of summer, however, the reaction would occur too slowly if it weren’t for the presence of a catalyst. The scientists therefore incorporated a catalyst into the matrix of the original composite used to construct the aircraft. When the liquid monomers flow out of the microcapsule, they come into contact with the catalyst, speeding up polymerisation by providing an alternative chemical route to the reaction. This reduces the speed at which the monomers must collide to join together. What’s more, the catalyst is not used up in the reaction, so it can be used again and again.
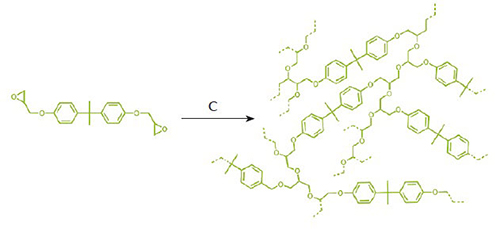
Image courtesy of Duncan Wass
As well as repairing the damage, it is possible to cause a colour change at the same time. The microcapsules could be designed to leak a colour when ruptured, signalling the area of repair. In reality, however, a big red mark showing where the aircraft wings have been repaired might result in some panic from passengers on-board the aircraft!
There is still a lot of testing to do before this technology can be applied in aeroplanes, not least because of the very stringent safety consideration for this application and because the healing agents must be stable enough to last the lifetime of an aircraft. However, there are many other consumer items that are now made from similar composite materials, from bicycle frames to sports equipment, and the application of ‘self-healing technology’ could soon become commonplace.
Review
This article illustrates how chemists and materials scientists can mimic natural processes to provide solutions to serious problems. It brings concepts like polymerisation to a practical level that students will identify with. It could be used as the basis of several discussions on topics such as:
- How technologists can learn from processes in nature.
- The importance of chemistry in everyday life.
- How engineering and science need to work together to provide creative solutions.
Suitable comprehension questions include:
- How do monomers become polymers?
- How can catalysts help polymerisation processes?
- How does the repair process described in this article mimic natural biological processes?
Marie Walsh, Ireland